Ensuring rigorous electronics quality control is at the core of our mission at PC Components Europe (PCE). Our quality control lab , recognized by engineers as one of the best in the industry, is equipped with state-of-the-art technology. This enables us to provide high-quality components to our clients and also support the training of future engineers .
In today's post, we will show you our step-by-step process in our in-house quality control laboratory. We'll also explain what a quality department is and why quality control is so important to us and our customers.
Read on to discover why we are proud of our quality laboratory at PCE!
What is a quality department in the electronics and electromechanical components industry?
The quality department within a company specializing in electronic and electromechanical products ensures that all items meet or exceed established quality, reliability, and performance standards.
This maintains the company’s reputation, ensures compliance with regulatory requirements, and enhances overall customer satisfaction.
Key responsibilities include implementing quality assurance policies, conducting audits, performing inspections and tests, managing supplier quality, driving continuous improvement, and proper maintenance of photos and documentation.
The Importance of Electronics Quality Control
In the component industry, the quality control is paramount for many reasons. Reliability, performance and safety of electronic and electromechanical systems are highly dependent on the quality of the components used.
High-quality components reduce the risk of system failure, maintenance costs and potential safety hazards, which are key considerations in industries such as aerospace, automotive, medical and consumer electronics.
They are also essential for the reliability, performance, and longevity of the electronic and electromechanical systems.
Poor-quality parts can lead to system failures, increased maintenance costs, and potential safety hazards, that’s why our quality control is at the heart of what we do at PCE.
We ensure that every component meets rigorous standards before it reaches your projects. From heavily vetting suppliers to in-house testing, we leave no room for compromise. Our goal is to determine if the devices are reliable, safe, and work as expected.
The Quality Department of PCE
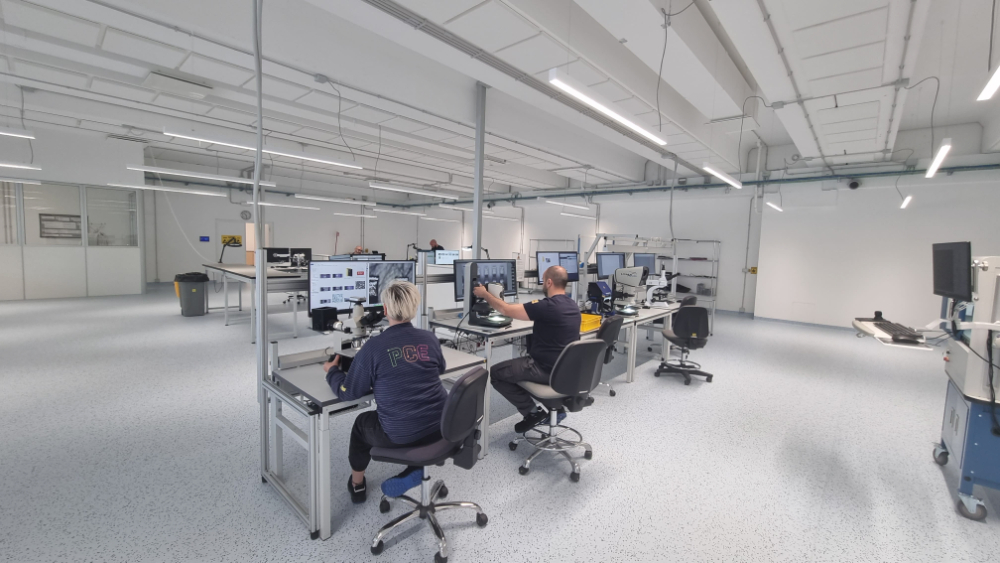
Our quality department plays a pivotal role in ensuring that every component meets rigorous standards. The processes encompass several key steps. We conduct comprehensive testing to verify the electrical characteristics and physical integrity of each component.
We ensure you receive genuine, high-performance parts, reducing the risk of counterfeit products entering your supply chain.
Moreover, our stringent quality checks are designed to meet and exceed international standards, such as checks according to the IDEA Inspection Standard IDEA-STD-1010B, which recognizes our quality-oriented business practices and operational excellence.
We are also certified under ANSI - ESD S20.20, ensuring the protection of electronic components from electrostatic charges, and AS9120B, the aerospace standard for distributors of components.
Additionally, our memberships in IDEA, ERAI, and Assodel, as well as our Legal Rating and training certifications, underscore our commitment to the highest levels of quality and reliability in the industry.
For more detailed information, visit the PCE certifications section on our website.
This is how we do it at PCE Quality Lab: Step-by-step
At PCE, we have implemented the IDEA STD-1010-B standard, recognized globally as the leading standard for incoming inspections in the electronics industry. Click here to see the PCE checklist for all incoming parts.
Step 1: Receiving Components from Suppliers
Upon receiving components from our trusted suppliers, we kick off the quality process. Our team enters the quality laboratory, donning antistatic clothing and shoes.
Step 2: Careful Unpacking and Initial Testing
We meticulously open the packaging, paying attention to every detail. The first step of the inspection verifies that the paperwork, labels, quantity, part number and part type provided with the shipment match the purchase order. This step also includes recording the packaging type, its condition, and the country of origin (COO), date code, and MSL level.
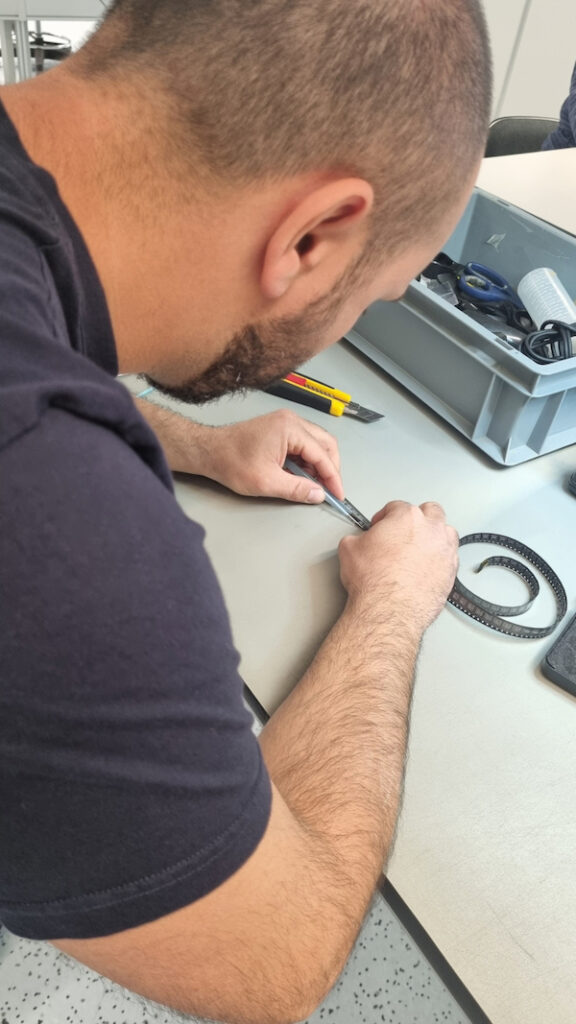
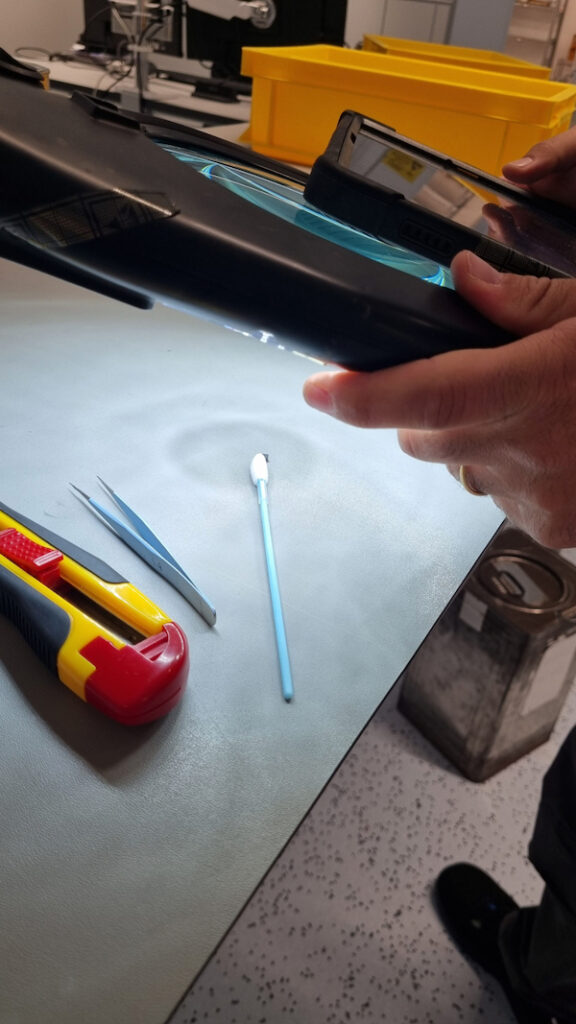
Our quality department takes photos along the way at every step: Upon shipment receipt, throughout our quality inspection, and again during outbound shipment. Our archive dates back to 2008 and a QC report can be provided upon request at any time.
Step 3: Part counting and Quantity Verification
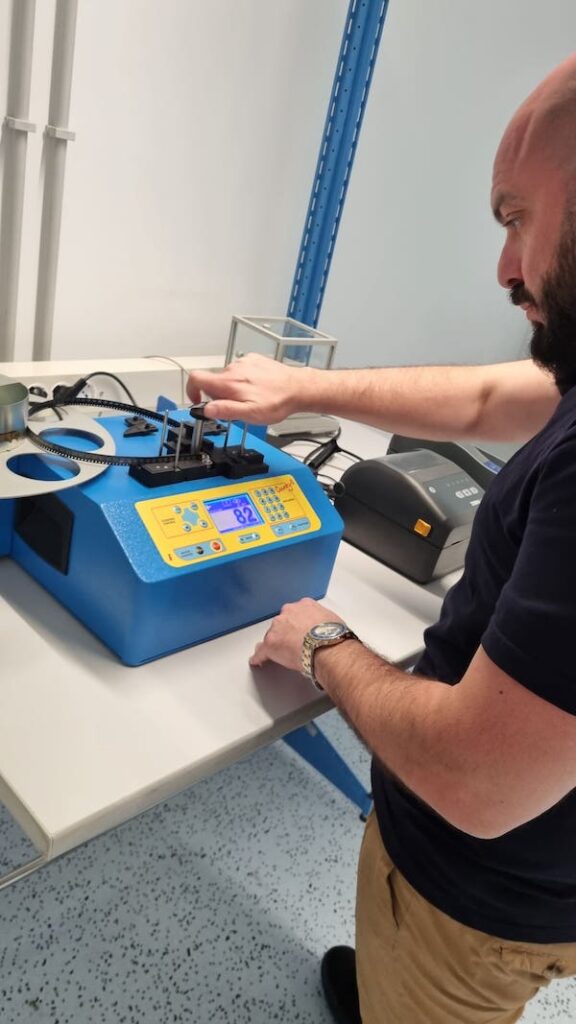
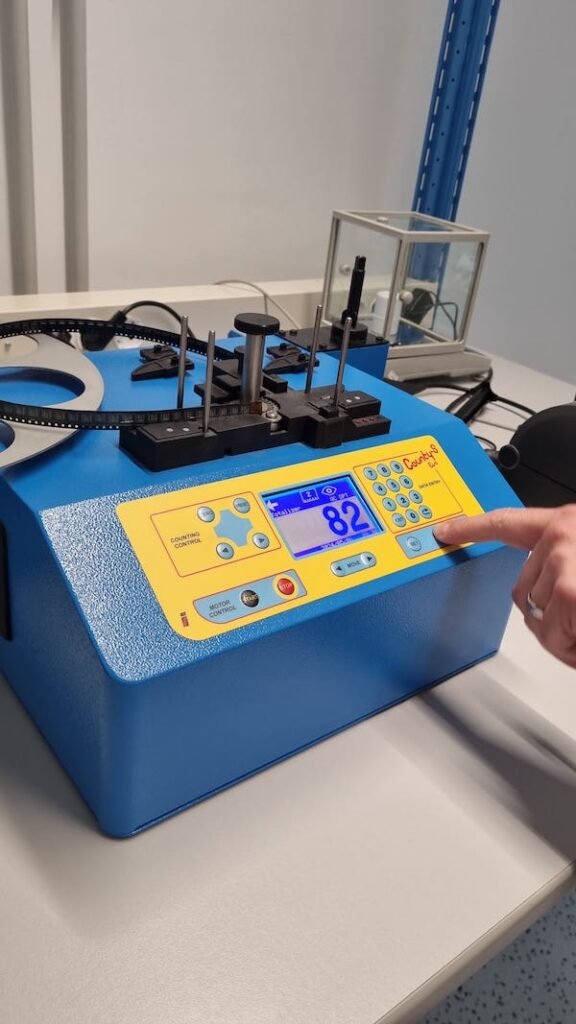
Accurate counting ensures precision in our inventory management. We use a reel-to-reel counting machine to verify part quantity when parts are received in tape carriers. Diligent visual inspection and pen counters are used for smaller cut tape quantities, trays, bulk, and all other packaging types.
Step 4: Advanced Visual Inspection
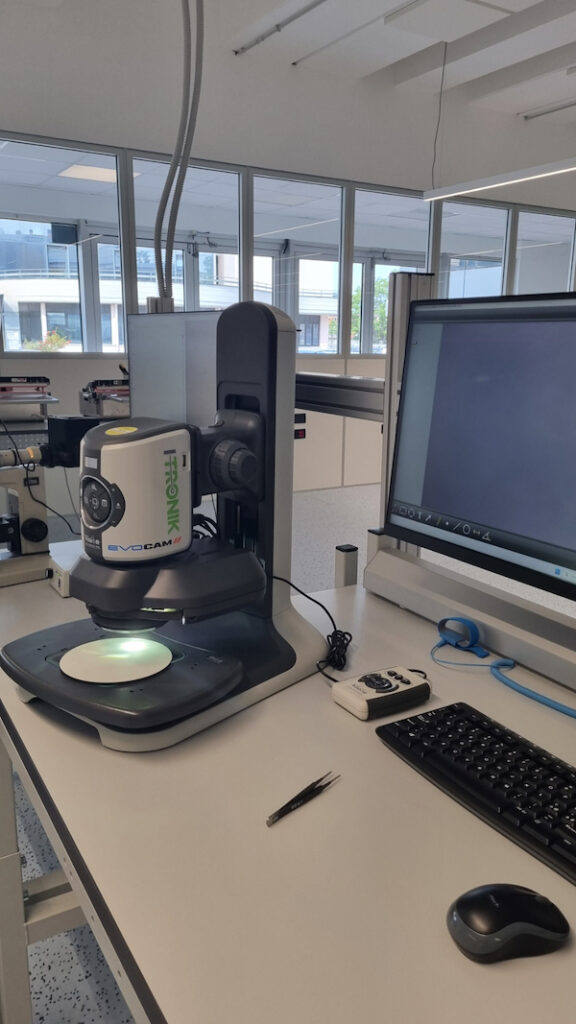
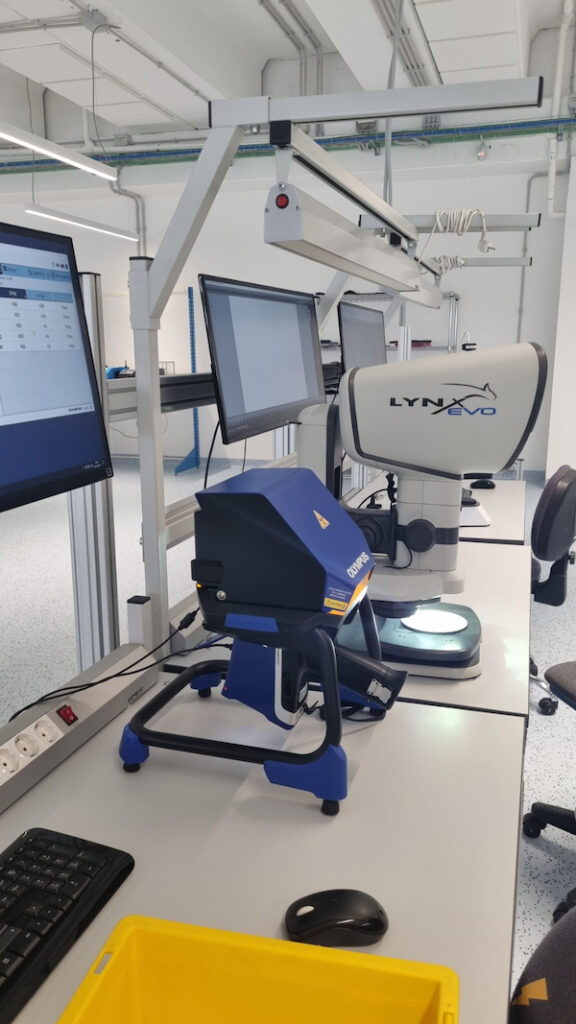
Our high-resolution microscopes allow us to distinguish new, used, and potentially counterfeit components.
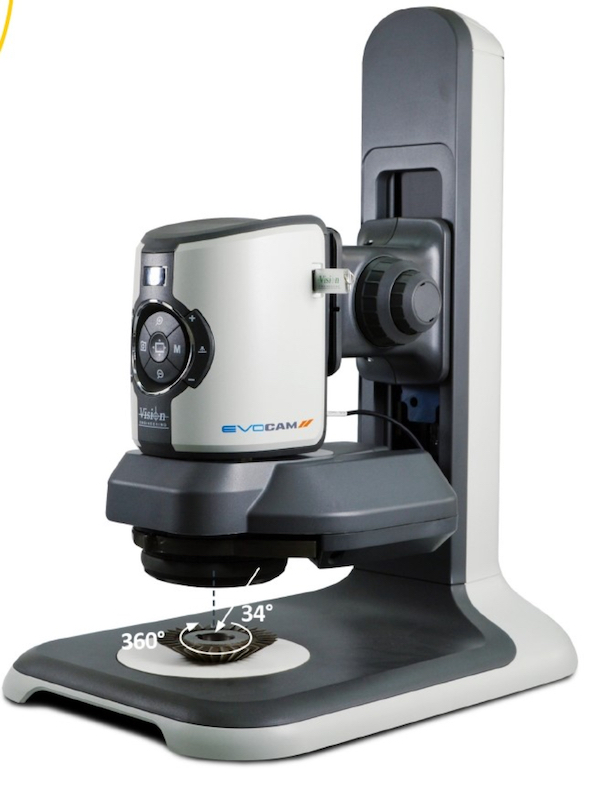
Excellent optical performance makes EVO Cam II a powerful imaging solution, with a range of options to ensure exceptional clarity for any application. Intuitive design simplifies operation and minimizes training requirements, making EVO Cam II a powerful and flexible tool, ideal for multiple applications, users and a variety of environments.
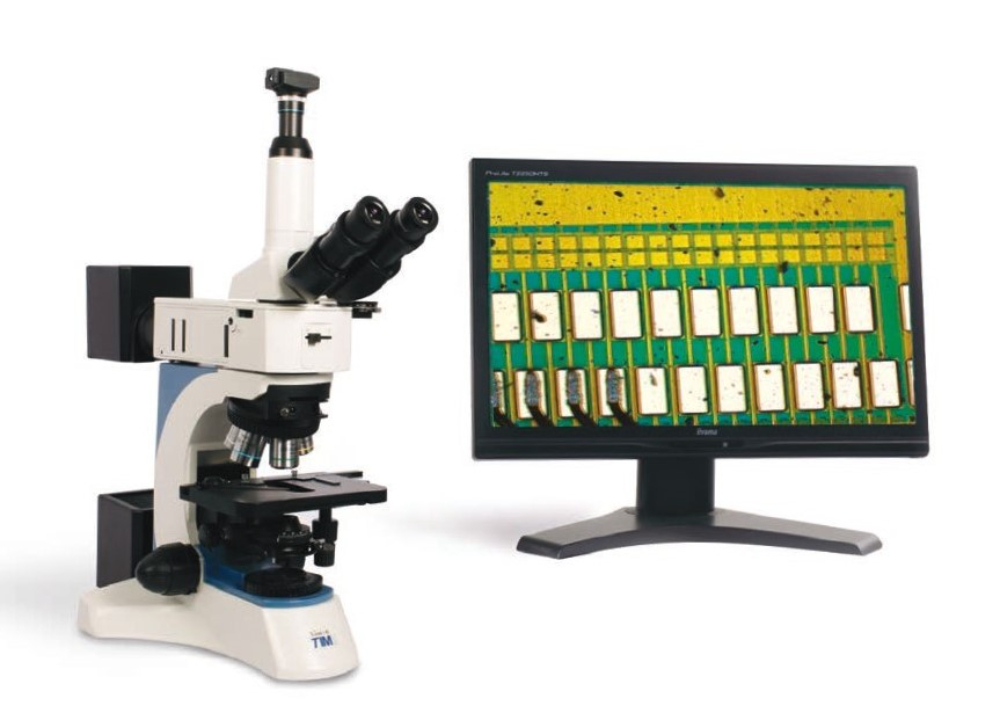
Whether you want to inspect alloys, plastics, ceramics or other materials, the TIM5 allows both novice and expert users to obtain detailed analyzes of a wide range of materials.
Our trained technicians, certified by the IDEA (Independent Distributors of Electronics Association), conduct thorough inspections.
Step 5: X-ray examination with state-of-the-art Technology, the X-ray and XRF Spectroscopy
Our commitment to quality extends to cutting-edge technology.
X-Ray and XRF (X-ray fluorescence) spectroscopy provide deeper insights into component integrity. X-ray examination allows us to view the internal construction of a part. In doing so we are able to detect broken or missing bond wires.
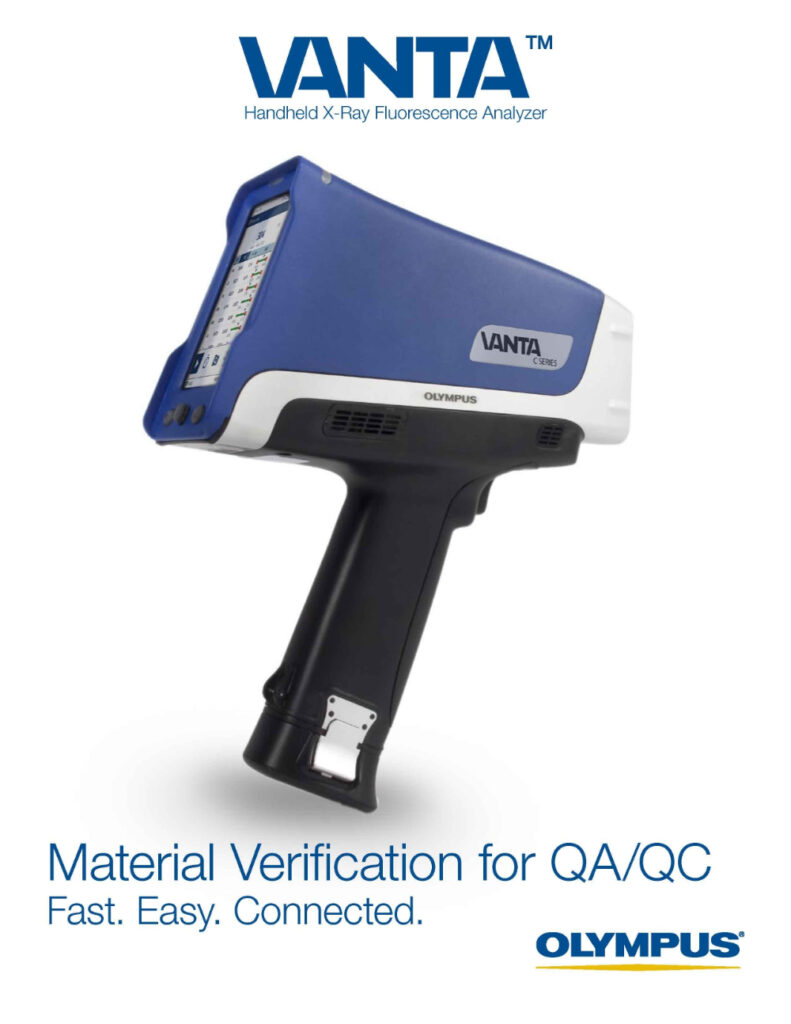
We have the new generation of Vanta handheld XRF analyzers that combine exceptional accuracy with speed and durability.
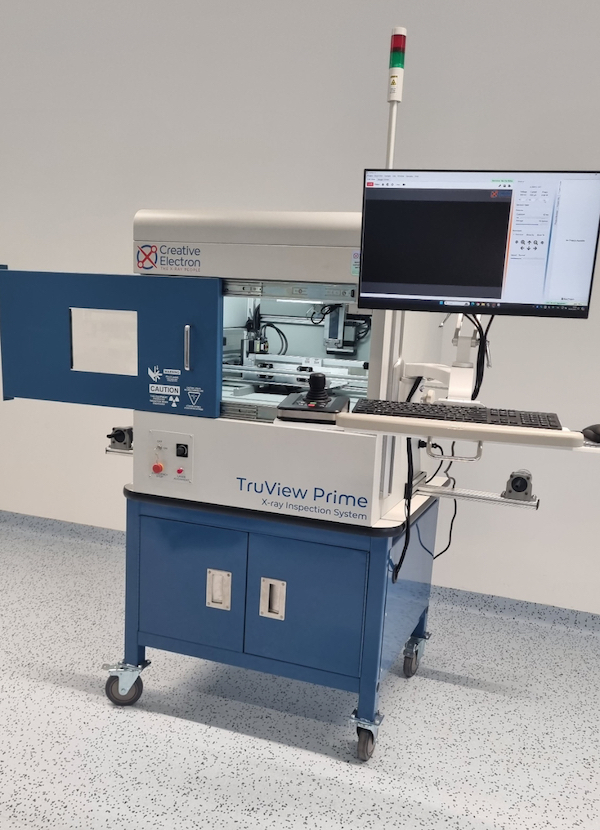
We also have TruView™ Prime which offers exceptional image quality and full automation.
We are also able to verify the existence of a Die where applicable. X-ray vision also allows us to compare parts among different lots, to a known golden sample or to other previous photos in our archive.
XRF analysis is a non-destructive method of elemental analysis used to detect the presence of certain elements/compounds and to measure their thresholds for compliance to manufacturer specifications and environmental legislation such as Reach and Rohs.
High-powered microscopes, stereo digital full HD and metallurgical, allow our IDEA qualified inspectors to study a components' surface, pin condition and markings.
Our inspectors qualify parts according to Pass, Fail or Inconclusive and are diligent detectives when it comes to researching datasheets, and comparing parts, labels and documents in order to confirm parts we supply are original, new and unused.
Step 6: Antistatic Packaging and Logistics
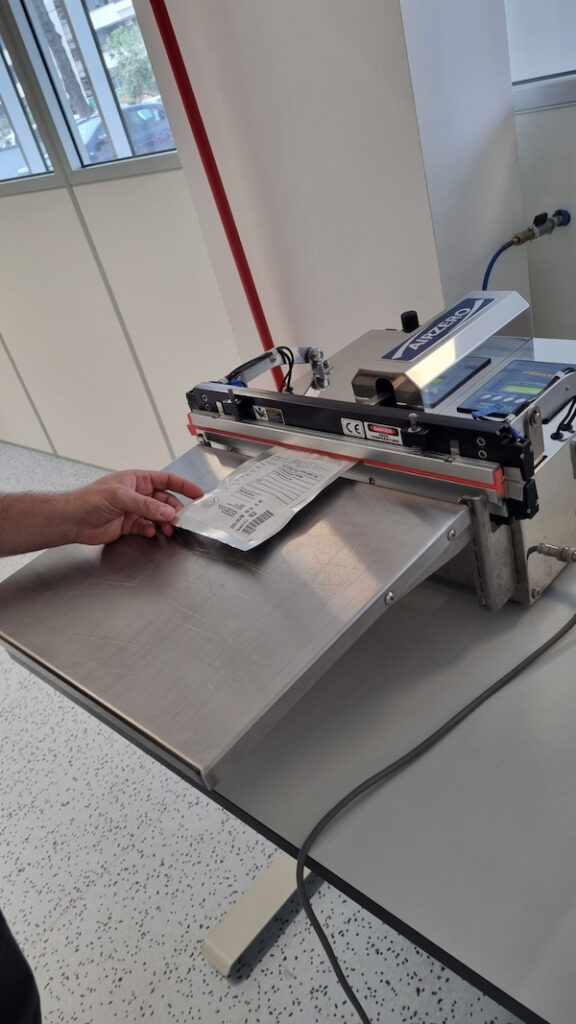
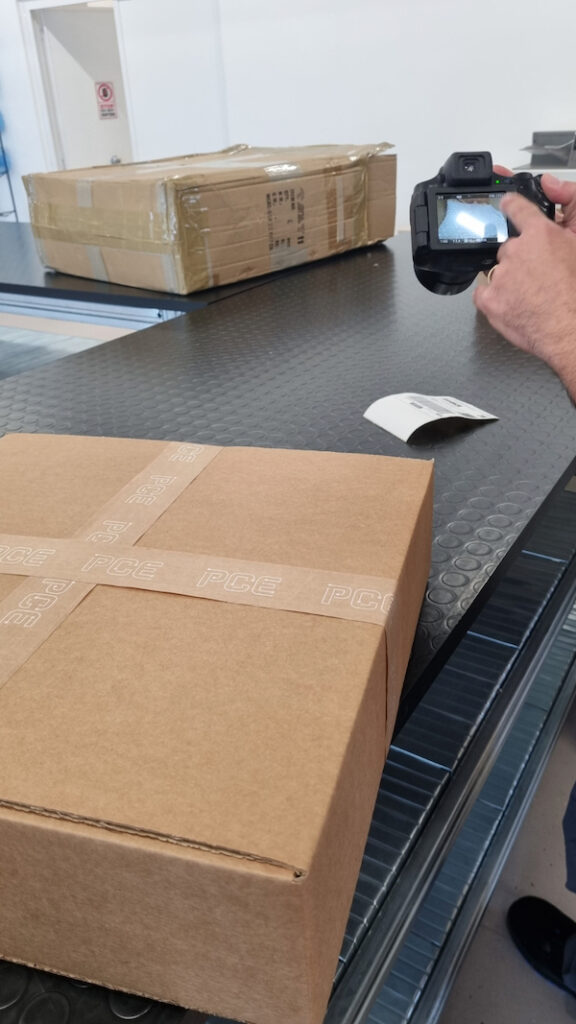
Components are carefully repackaged in antistatic and/or moisture-sensitive barrier bags according to their MSL Level and following Jedec standards.
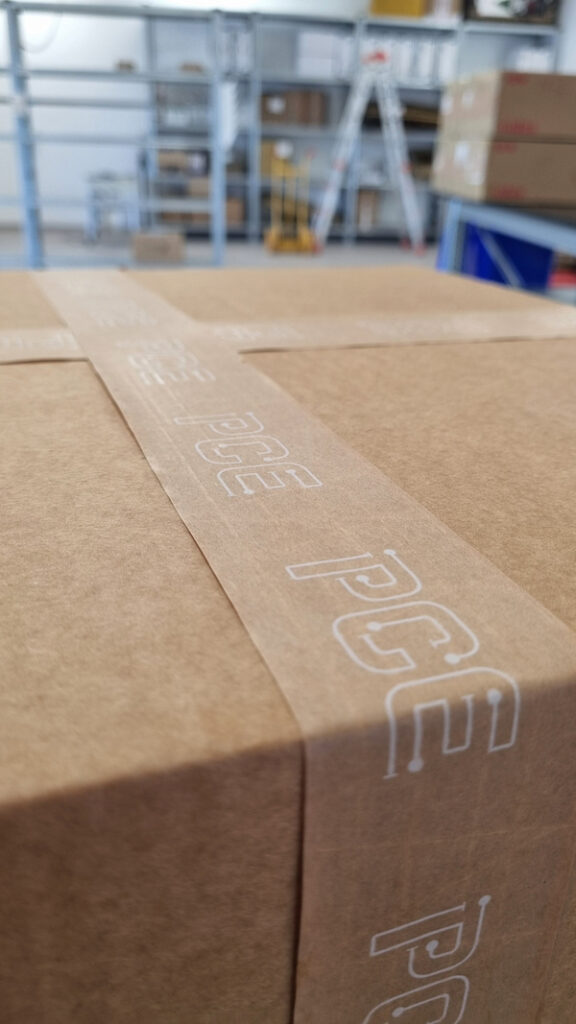
They then proceed to our logistics department for meticulous packaging and shipping.
Advantages of Quality Control in the Components Industry
These advantages are some of the reasons why electronics quality control is central to our mission at PCE.
-
- Higher Reliability and Performance: Ensures components meet stringent standards, leading to superior reliability and performance in the final product.
-
- Enhanced Safety: Reduces the risk of component failures that could lead to safety hazards, particularly critical in industries like aerospace and medical devices.
-
- Increased Customer Trust and Satisfaction: Delivering high-quality components boosts customer trust and satisfaction, fostering repeat business and a positive reputation.
-
- Cost Savings: Prevents costly rework, repairs, and returns by catching defects early in the production process.
-
- Regulatory Compliance: Guarantees adherence to international and industry-specific standards, facilitating smoother market entry and regulatory approvals.
-
- Traceability Recording and Accountability: Provides detailed records and photos of each component’s history, ensuring transparency and accountability in the supply chain.
-
- Counterfeit Detection: Rigorous quality control processes help detect and eliminate counterfeit components, protecting the integrity of the supply chain.
-
- Supplier Improvement: High standards encourage suppliers to improve their processes, fostering stronger and more reliable partnerships.
-
- Innovation and Process Improvement: Continuous quality assessments drive innovation and improvements in manufacturing processes and product designs.
-
- Durability and Longevity: High-quality components contribute to the durability and longevity of the final product, enhancing its overall value.
“Our commitment to electronics quality control defines us at PC Components Europe. It’s not just a checkbox, it’s the heartbeat of our operations, driving innovation, reliability, and client satisfaction.”
– Annie, Founder of PC Components Europe
When you choose PC Components Europe, you're not just buying components, you're investing in peace of mind
Our unwavering commitment to quality means that you can trust our parts to deliver exceptional performance, enabling your projects to succeed and innovate without setbacks.
Experience the difference that meticulous quality control makes – choose PC Components Europe for your electronic and electromechanical needs.
Do you want to know more about our Quality Lab?
Schedule a visit and learn more about PC Components Europe's internal lab!
We will be glad to assist you in a personalized way!
Contact PC Components Europe:
Telephone: +39.06.7696.8780
Address: Via Orazio Raimondo, 47 Rome 00173 Italy
Follow us on social media: LinkedIn